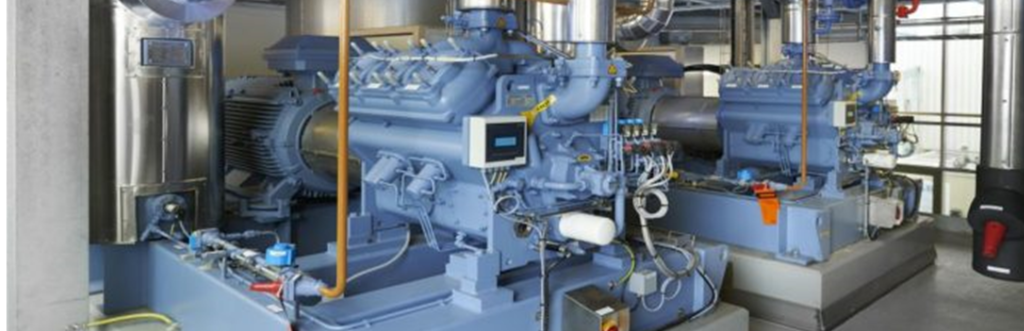
Electrifying industry with heat pumps
Electric heat pumps are a promising alternative for an efficient and emission-free supply of process heat at technically feasible temperatures, with potential to push the envelope up to over 200 degrees.
Summary: Heat pumps are not just for heating our homes, they can play an important role in decarbonising industry. Despite electric heat pumps being a promising alternative for an efficient and emission-free supply of process heat at technically feasible temperatures, industrial heat pump (IHP) deployment has been limited. But is that about to change?
Why this is important: This is a market where Europe and Japan could gain competitive advantage.
The big theme: Heavy industry is responsible for approximately 20 per cent of global CO₂ emissions, plus process industries are also major consumers of energy, making them primate candidates for electrification. The sheer scale of the net-zero electricity and/or hydrogen required means that it will take decades to implement the new technologies we require, attracting billions of dollars in investment and generating thousands of new jobs. Products such as ‘green steel’, made using hydrogen rather than coal, represent a huge opportunity for investors.
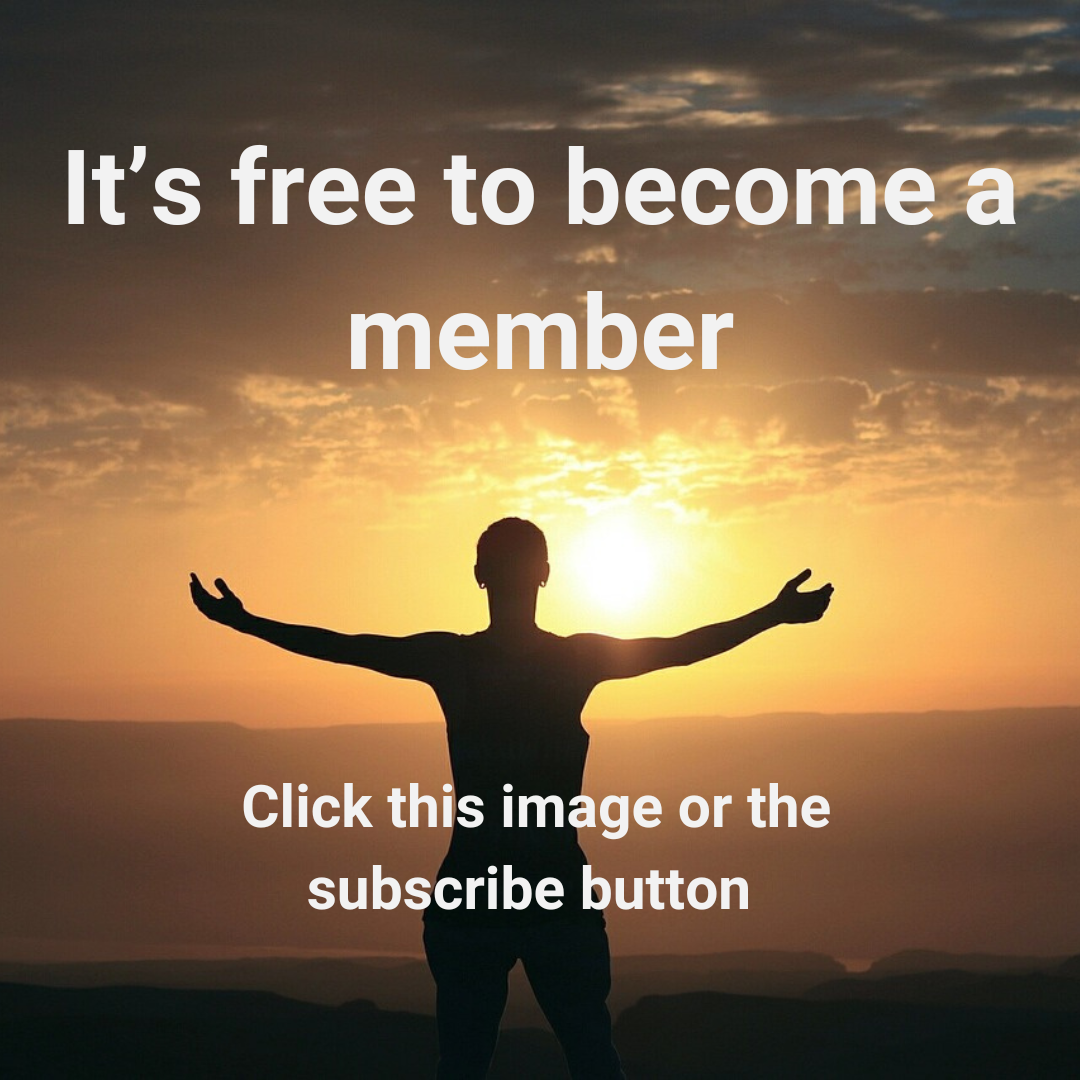
The details
Summary of a story from Berkley Labs:
Thermal processes in U.S. manufacturing are responsible for approximately two-thirds of total final energy demand. Decarbonization of industrial heat demand through electrification could contribute significantly to climate change mitigation efforts. Electrification technologies that are applicable to a range of industrial processes, without needing major modifications to the existing infrastructure, may help facilitate the clean energy transition.
Electric-driven heat pumps are among those technologies that are suitable for process heat supply in a sustainable manner, while also improving the overall energy efficiency. However, despite them being a promising alternative, industrial heat pump (IHP) deployment in the U.S. has been slow.
Why this is important
Heavy industry is responsible for approximately 20% of global CO₂ emissions. If we ignore for a moment feedstock for chemical plants, approximately three quarters of the energy requirement is for heat or reductants (chemical reducing agent). This requirement is currently supplied almost entirely from fossil fuels owing to their low cost and wide availability. This is a big part of what makes heavy industry so emissions intensive. Plus, what we think of as process industries, beer production, food processing, textiles, and ingredients, are also currently major users of fossil fuel energy. Industrial Heat Pumps (IHP's) are able to help solve part of this challenge. They can upgrade the temperature of a waste heat source, allowing previously waste heat to be reused. This can result in large savings in energy consumption and cut greenhouse gas emissions.
Despite the large potential for energy and CO2 emissions reduction in manufacturing, there are several barriers associated with the wide-scale applications of Industrial Heat Pumps . Some of this is due to cost, with the average electricity price for U.S. industry (i.e. 70 $/MWh) being almost 5 times higher than the average price of natural gas (i.e. 14 $/MWh) (2021 data). There is a similar challenge in Europe, compounded by the fact that generating electricity with expensive gas is now the price setter in most markets.
Outside of the cost issue (solvable with government assistance and dedicated lower cost renewable generation), it has been argued that the main adaption barrier relates to a shortage of heat pump suppliers, especially for higher temperatures. There are several IHP manufacturers on the market that can provide heat sink temperatures of up to 90°C, however there are only a limited number of steam generating IHP suppliers (requiring temperatures over 120 degrees). These include Mitsubishi, Siemens, and MAN Energy.
The Berkley Labs report argues that this creates a chicken and egg situation. There are few suppliers, so most plant process operators have limited knowledge of what IHP's can deliver. Plus, its seen as a new, and hence "risky" technology. So IHP's don't get specified as a solution, which means there is limited incentive for suppliers to develop new products that could be used more widely ... and around we go again.
This is a market where Europe and Japan could gain competitive advantage, and it does appear that change is happening faster than you might think. This Cleaning Up podcast (by Michael Liebreich) is worth a listen if you want to understand some of the recent advances. There is also a lot happening on the political side. The EU-funded PUSH2HEAT project aims to identify solutions to the technical, economic and regulatory barriers, looking at applications up to 200 degrees C, which would cover up c. 37% of the process heat required by European industry. There will be four demonstration projects, covering the food, paper and chemical sectors. This is clearly not going to happen quickly, but we argue that strategically it makes sense for companies to start development now, tapping into government funding. Those companies that get ahead of the curve on this will be well placed to exploit the long-term growth opportunities.
Something a little more bespoke?
Get in touch if there is a particular topic you would like us to write on. Just for you.
Contact us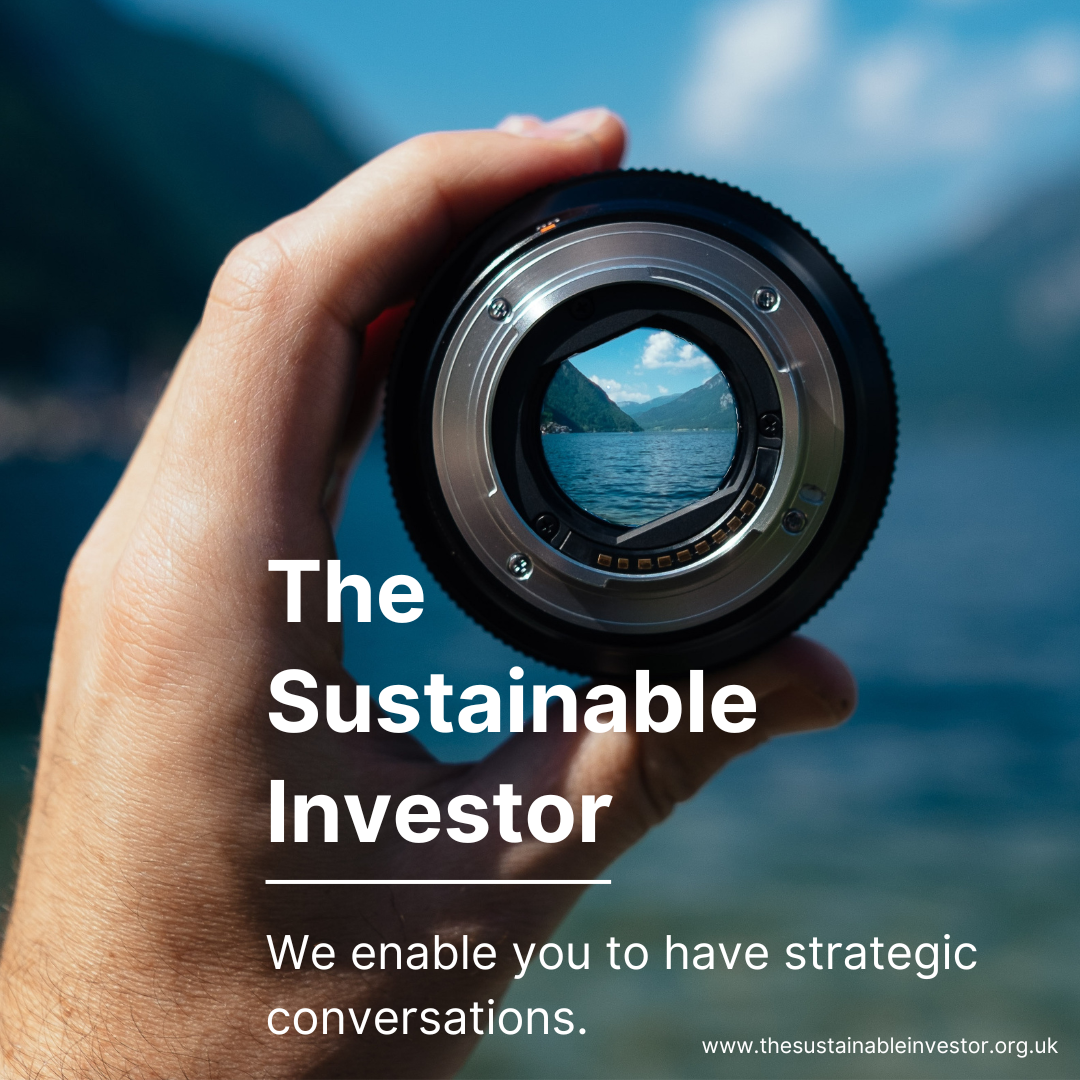
Please read: important legal stuff.