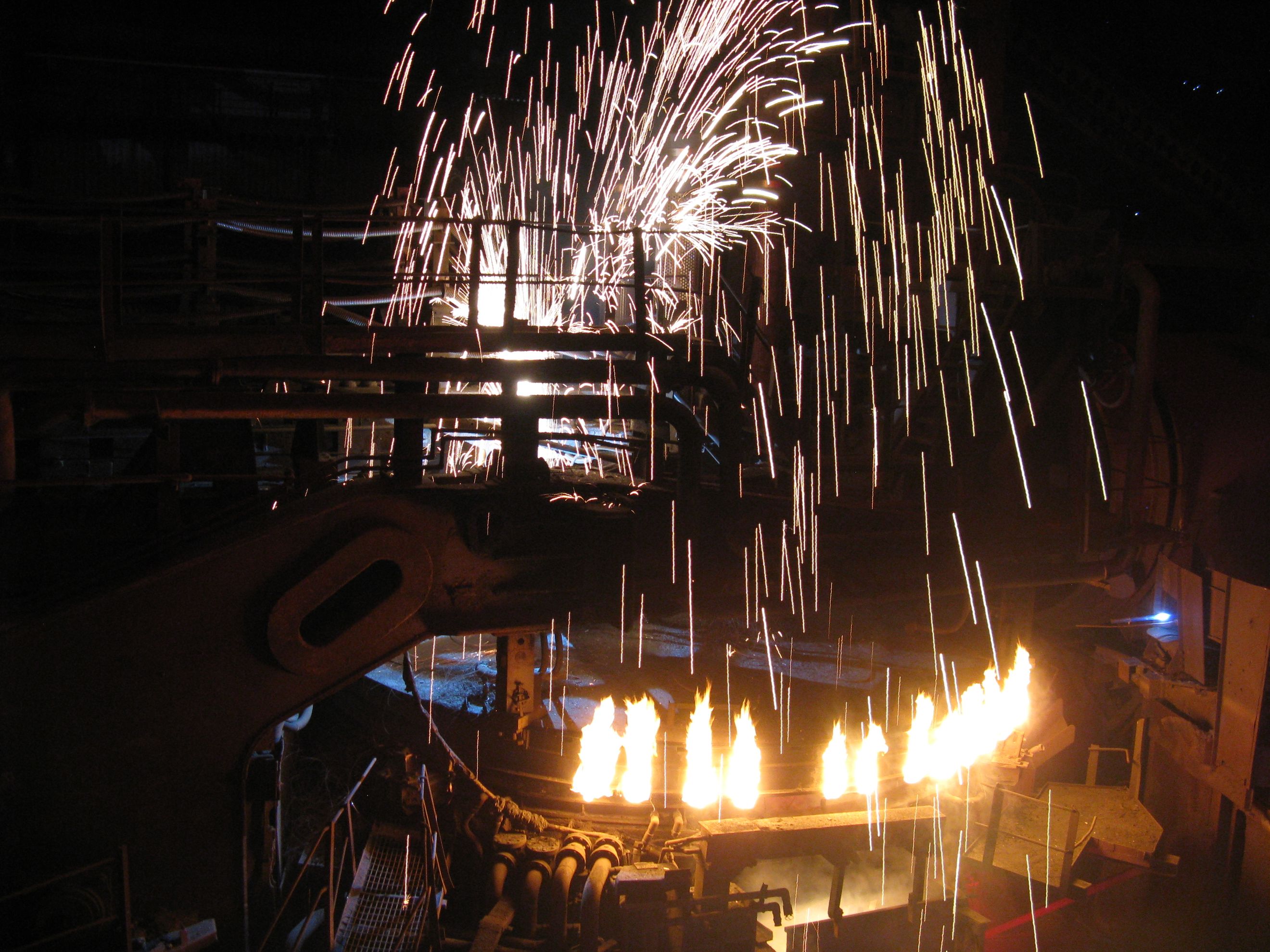
Pathway to green steel
Steel is a fundamental building block of our modern economy. As a large source of GHG emissions, its production is an important decarbonisation problem. But we have solutions.
Summary: The IRA and the IIJA provide powerful incentives to mobilise the US steel industry towards near zero emissions production. As a critical commodity for construction and other major industrial uses, as well as a large source of GHG emissions, steel production is an important decarbonisation problem.
Why this is important: Solutions do exist but they will require partnership building both on the supply and demand side to ensure economic scalability.
The big theme: Steel is a fundamental building block of our modern economy. It is used extensively in construction, automotive and transportation as well as energy, infrastructure and machinery.
Steel is an alloy of iron and carbon with small amounts of other elements producing varying properties - for example stainless steel which contains chromium doesn't rust or corrode as easily as other forms of steel.
Whilst almost 90% of steel is recycled, the steel industry is still responsible for about seven percent of all man made global greenhouse gas (GHG) emissions and so is an important decarbonisation problem that needs solving.
Steel is currently produced via two main routes:
- Blast Furnace-Basic Oxygen Furnaces (BF-BOF): Coke (coal that has been heated at high temperature for a day, then cooled) and iron ore (in the form of sinter) are fed into a blast furnace and then hot air at 1,250oC is blown in from below. The iron ore is 'reduced' (its oxygen is removed) to produce 'pig iron' and a waste product called slag. The amount of carbon in the pig iron is reduced by mixing in scrap steel and then blowing oxygen in to produce crude steel. Between 70 -75% of current global steel production comes from the BF-BOF method.
- Electric Arc Furnaces (EAF). A mixture of scrap steel, Directly Reduced Iron (DRI) and quicklime (calcium oxide) is preheated (often using heat from the previous cycle of steel making). This mixture or 'charge' which can be fully scrap or fully DRI, is put into the furnace and graphite electrodes inserted and an electric current passed through them creating an arc (plasma) which melts the charge at a temperature of up to 3,000oC. The process is repeated a number of times and then oxygen is injected to reduce the mixture to steel. The EAF technology, which uses mainly recycled scrap steel, is seen as better for the environment as it produces materially fewer GHG emissions. But, there is not enough recycled steel to meet growing demand using the EAF steel making method alone. DRI could take up the bulk of the shortfall in scrap. The iron is reduced using syngas, a mixture of carbon monoxide and hydrogen. If the hydrogen is produced using renewables rather than from fossil gas, then emissions are even lower.
What are the financial considerations?
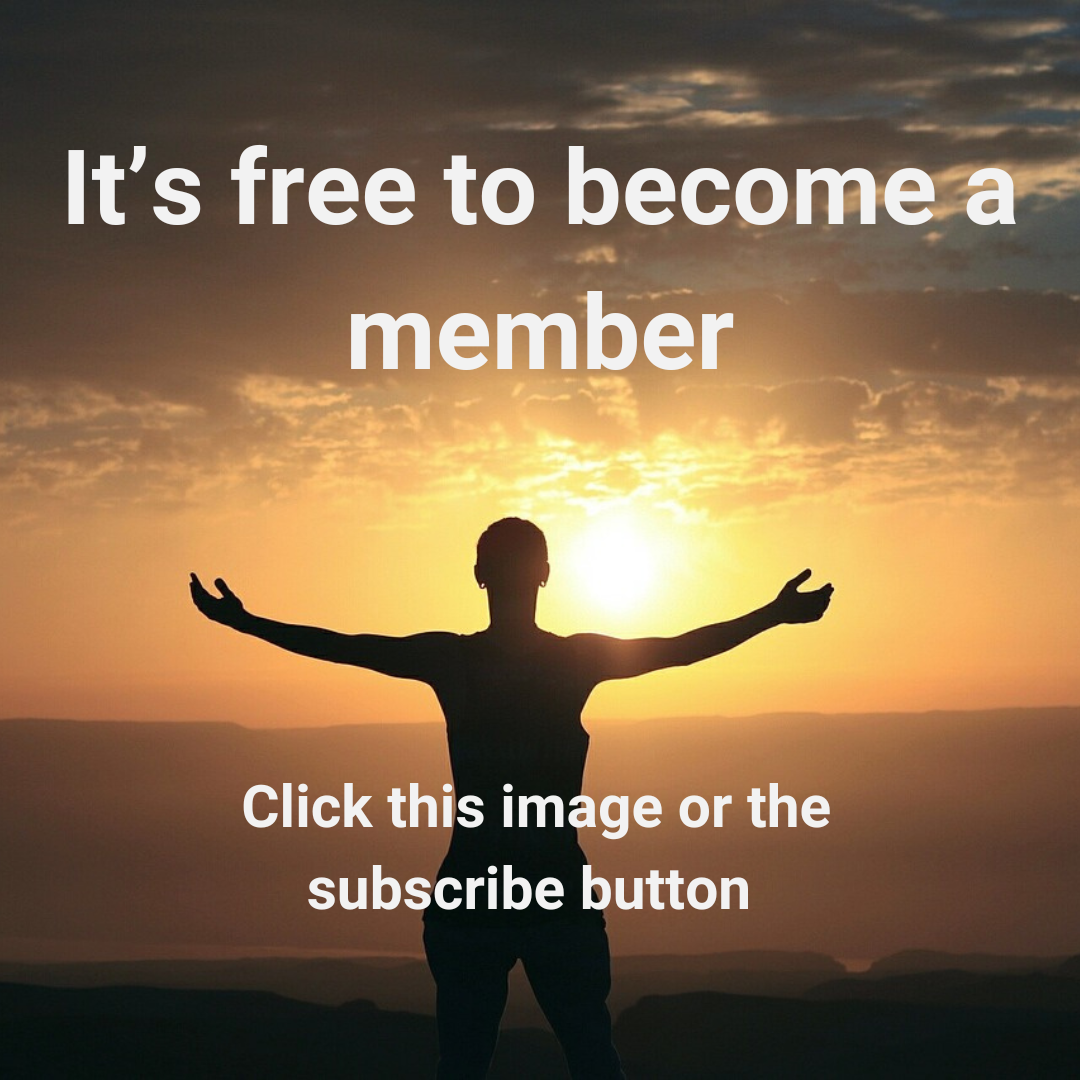
The details
What are the financial considerations?
The steel making process, like many heavy industries, is incredibly complex. It's not just a case of throwing some iron ore, coking coal, and quicklime into a furnace. Companies have invested a lot in accumulated knowledge and infrastructure. This is a capital intensive industry with relatively low margins and returns on capital employed. Developing new processes to create green steel, even if they might look broadly similar to processes used now, is a material risk for the companies involved. Changing processes from what they know to something new is a material "step into the dark". Learning how to create green steel in a cost effective way will involve hundreds if not thousands of small improvements - fine tuning production processes, inputs and operating practices. This is an important factor to bear in mind - it's going to take time.
The challenges are however solvable. Some of the solutions require financial and other assistance from governments, as they seek to create benefits for the wider society that they represent. Important considerations include:
- Jobs: looking specifically at Europe -while the steel industry is nowhere near as important as it used to be, its still a decent sized employer. According to Eurofer data, the sector directly employs c. 325,000 people across Europe, with the biggest country being Germany (just over 83,000). If you add in indirect employment, the total number of jobs is claimed to be as much as 2.6m, with c. 500,000 of these being in Germany. The region produces over 177m tonnes of steel per year, c. 11% of global output. In terms of consumption, the biggest European end markets are the construction industry, automotive, and metal goods.
- Supply chain security: A 2019 report from Oxford Economics estimated that the four main steel customer groups (fabricated metal products, mechanical machinery, automotive, and construction) together contributed โฌ3,386bn in Gross Value Added (GVA) and supported over 62m jobs. To quote the report, "across all four sectors combined, almost one-third of their additional economic impacts could be thought of as being โenabledโ by EU steel". The biggest impacts were in automotive and machinery manufacturing (60%) and the smallest in construction (12.5%).
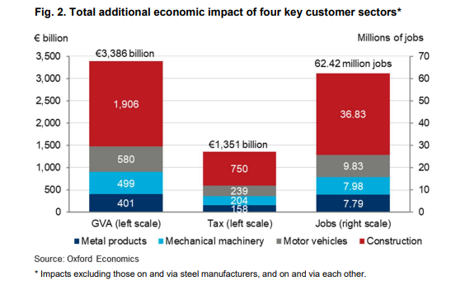
In 2022 Europe was estimated to have imported some 35m tonnes of finished steel products, of which the majority came from Turkey, South Korea and India. In the context of total European production (as above c.177m tonnes) this is not overly material. But you can see that, especially in times of supply chain stress, many manufacturers would be concerned if the level of imports rose substantially.
Summary of a report from RMI
Whilst the US has shifted to producing 70% of domestic steel through EAFs, iron-ore based steel making still largely requires coke, coal and fossil gas. The Inflation Reduction Act (IRA) and the Infrastructure Investment and Jobs Act (IIJA) should provide financial support to offer routes to near-zero emissions steel.
RMI focused on green hydrogen direct reduced iron electric arc furnace manufacturing (H2-DRI-EAF) as the most viable route and applicable to both iron ore and scrap-based production. The key steps recommended for producers are to (i) build partnerships across the steel value chain, building industrial hubs to gain scale and mitigate risk exposure, (ii) optimise federal funding opportunities and incentives with the end of September 2026 seen as a key date to stack those incentives from IRA and IIJA, (iii) look for new funding routes through sustainability and innovation funds, PE and VC as well as DOE programmes; and (iv) coordinate buyer procurement - buyer coalitions even - to build sufficient demand.
Other things to consider
There is only so much scrap available for use in steel production and so pig iron or direct reduced iron will have to be the main sources. According to McKinsey there are 24 new direct reduced iron plants with between 40 and 50 metric megatons of capacity announced in Europe as at the end of November 2022. However, that could require almost two Mt of hydrogen per annum. That is 10% of European forecast hydrogen demand in 2030! An alternative would be to 'bring the DRI' in from elsewhere. That would be in the form of Hot Briquetted Iron (HBI) which is DRI that has been put under very high pressure and temperature to form dense and very much less porous briquettes - much less reactive and so easier to transport. Of course there is a trade-off: Hot Direct Reduced Iron (HDRI) requires less heat than cold HBI (an estimated additional 100 to 150 kWh per ton to melt) as it is integrated and already hot! There would also be additional transportation costs of bringing in the HBI. When looking at lower emissions hydrogen, the costs of green hydrogen vary considerably across the globe. The gap between grey and green hydrogen in Europe is particularly high as you can see from this discussion ๐๐พ
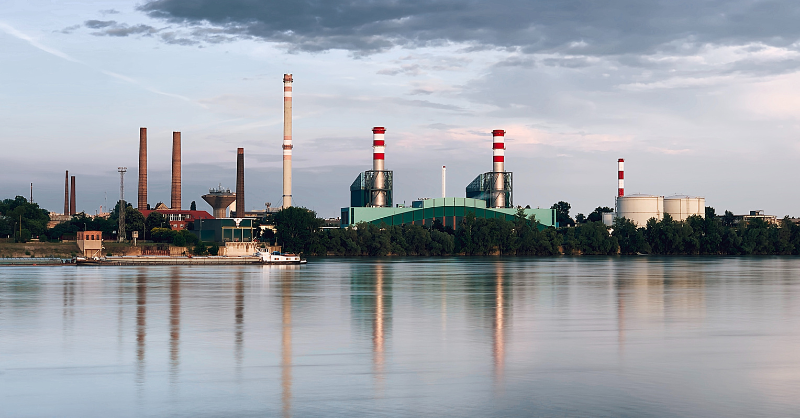
Outside of Europe, Liberty Steel, part of the GFG Alliance group bought the Australian Whyalla steelworks out of bankruptcy in 2017 and is now aiming to spend half a billion dollars installing an EAF powered by renewable power sources and a 1.8 million tonne Direct Reduction Plant which will eventually be transitioned to green hydrogen, although will use fossil gas initially. The owner Sanjeev Gupta claims that the plant will be able to reduce its direct CO2 emissions by 90% and be 'carbon neutral' by 2030. One worth monitoring given controversy with GFG Alliance's other projects, most notably in Scotland with the Lochaber smelter which included a substantial amount of public funds too.
There are a number of other emerging technologies at varying stages of development. HYBRIT is a technology that is a direct reduction process using green hydrogen as the reducing agent. The HYBRIT initiative was started by SSAB, LKAB and Vattenfall with financial support from the Swedish Energy Agency and EU's Innovation Fund. The demonstration plant is scheduled to start production in 2026. There are a number of very early stage initiatives using electrolysis to produce steel. Boston Metal with their Molten Oxide Electrolysis technology and Siderwin from ArcelorMittal are two examples.
Something a little more bespoke?
Get in touch if there is a particular topic you would like us to write on. Just for you.
Contact us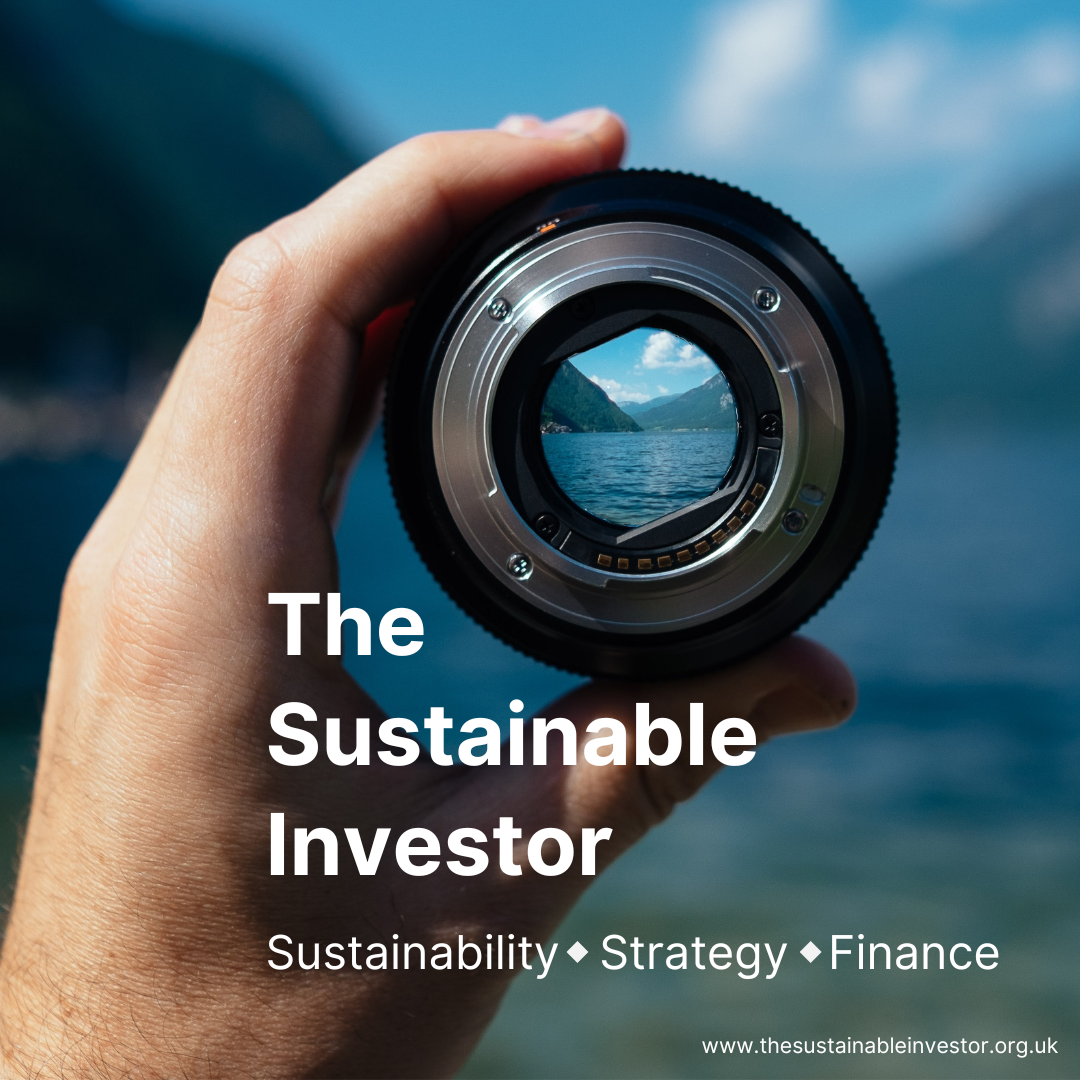
Please read: important legal stuff.